How to improve and optimize a business process, step by step
The processes that form the backbone of modern business operations require continuous improvement to stay effective and efficient. Here is a method for improving them.
As businesses grow and evolve, so do their business processes. Depending on the company's size, there are dozens, if not hundreds, of business processes that stakeholders inside and outside an organization participate in daily.
A business process comprises a sequence of steps that flow in a specific order to achieve a desired outcome. The process can be dedicated to activities such as new client onboarding, sales and marketing, customer support requests, order fulfillment, human resources, procurement management, and accounting.
As the business and business environment changes, these processes continuously evolve and need constant evaluation, improvement and optimization. Outdated processes can create customer and employee dissatisfaction, costly operational inefficiencies and loss of market share.
What is business process improvement and optimization?
Effective business process management (BPM) requires a well-thought-out plan that addresses the continuous needs for process definition, execution, evaluation and iteration. At the core of BPM is business process improvement and optimization -- an operational practice that identifies, evaluates and resolves business process problems and concerns.
Business process improvement and optimization aim to redesign an existing process to make it more efficient, streamline operations, upgrade communications, reduce errors and costs, and enhance workloads. These improvements should be continuous as businesses change, evolve, expand and implement new technologies.
There are several time-tested methodologies to improve and optimize business processes. The following techniques and tools place the customer at the center of a company's entire operation:
- Six Sigma has been around since the mid-1980s as a general approach to process improvement and total quality management. It uses the DMAIC -- define, measure, analyze, improve, control -- concept as a framework to make continuous process improvements. This data-driven methodology focuses on process improvement through precise measurements and rigorous analysis, aiming for near-perfection in performance.
- Lean thinking is a modified version of Six Sigma. It focuses on specific tasks that deliver more value to customers and identifies areas of potential process inefficiencies. It identifies non-value-adding activities and eliminates them, streamlining operations to improve quality and efficiency. Lean principles have transcended manufacturing. They are being applied in various sectors, including services, to enhance processes by reducing waste, optimizing workflows and efficiently delivering value to customers.
- Total quality management (TQM) was popularized in the 1980s by manufacturers and government agencies. It focuses on eliminating process defects and improving the overall quality of the final product or service. TQM is a holistic approach focused on continuous improvement in all aspects of an organization's operations. In organizations adopting TQM, all members participate in improving processes, products, services, and the culture in which they work.
Why are efficient business processes important?
All companies recognize the value of efficient processes, but the reality is that many businesses encounter workflow inefficiencies that need to be corrected. As enterprises digitally transform in today's highly competitive business landscape, inefficient processes can negatively impact a company's entire business operations. Just one inefficient process can affect resources, the workforce, profits, and the quality and reliability of products and services. Inefficient processes can create bottlenecks that hinder operations, increase costs, force missed deadlines and uncompleted tasks, and slow an organization's reaction speed to market swings.
In a rapidly changing world, optimizing business processes is not just a strategy but a necessity for survival and growth. Processes need to be constantly updated so that organizations aren't caught off guard. Organizations need to adapt swiftly to market changes, technological advancements and evolving customer expectations, which are all moving at an unprecedented pace.
Efficiently streamlined processes help organizations respond with agility, reducing time-to-market for new products or services and ensuring they remain competitive. Moreover, optimization often involves the integration of digital tools and technologies, which can lead to enhanced data analysis and decision-making capabilities. This digital transformation helps businesses anticipate market trends, improve customer experiences and innovate continuously. Flexible, optimized business processes are a key element to organizational agility.
Keeping these processes up to date, improving them as needed and continually optimizing them, however, can be difficult. People are often resistant to change, especially when processes have been in place for a long time. It's important to communicate the purpose and benefits of improving a business process to the relevant stakeholders.
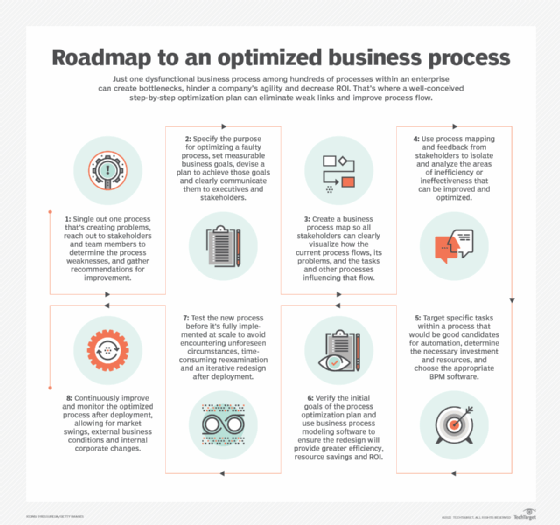
What are the benefits of optimizing business processes?
A process that's well managed and continuously improved can reduce errors, shorten process completion times, enhance workloads, identify waste, eliminate duplication and increase overall business performance. Optimizing a business process can also increase consistency, quality and compliance; reduce risks; and provide greater visibility for customers and executives.
Steps to improve and optimize a business process
When planning a business process improvement initiative, determine what the business goals are, where improvements are needed and what needs to be optimized. A goal-centric vision sets the foundation for measuring and evaluating progress.
1. Identify a single process that needs improvement no matter how small
Focus on one process that needs immediate improvement, reach out to stakeholders and team members to determine which tasks and activities take the most time and resources, and gather recommendations on how the process can be improved. Within that process, choose a task that's the least complex and time-consuming to optimize but will show immediate ROI regardless how small it is. Small optimization projects can still show significant results, provide easy wins for stakeholders and gain companywide buy-in for more complex process optimization activities.
2. Set business goals for your process improvement project
Once a process has been identified for improvement, define the purpose of optimizing the process; set the overall goals and smaller, immediately measurable goals; and devise a plan to achieve those goals. Have a clear understanding of what optimization will achieve -- for example, financial savings, resource savings or time savings. Clearly communicate these goals to executives and stakeholders so everyone is in agreement.
3. Create a map of the existing process
Visually map the business process using BPM and business process modeling methods that have been popularized over the last few decades. These tools can provide an easily understood, standardized way of defining how a current process flows through different departments, the various steps within the process, and the components within processes that run sequentially or in parallel.
4. Analyze the current process to isolate weaknesses
Process mapping helps analyze the current process and locate areas of inefficiency or ineffectiveness that can be improved and optimized. Use the feedback provided by stakeholders to analyze which steps in the process take the most time, create bottlenecks, cause communication breakdowns, fail to provide value and can be reworked or eliminated. Optimization might involve making some tasks conditional, integrating certain tasks, adapting data permissions and automating manual tasks.
An emerging class of AI-powered tools are stepping in to provide insights into which business processes might be bottlenecks and which can be potentially optimized to realize improved gains.
5. Target specific tasks for automation
Automation provides opportunities to quickly improve and optimize a business process by eliminating manually caused bottlenecks, addressing repeatability and quality issues, and removing inefficiencies. Determine what monetary and time resources are available to invest in business process automation software and whether the necessary tools already exist in the organization.
6. Verify the initial goals of the process redesign plan
Be sure the process redesign will meet the established business goals and significantly impact process efficiency, resource savings and ROI. Business process tools can help model and measure the impact and provide recommendations on where the process can be improved while still in the pilot stage.
7. Test the new process before fully implemented
Testing and quality assurance are equally important steps to ensure the new process will work before it's implemented at scale. Optimized business processes can often be hindered by unforeseen circumstances. Testing the entire process before full implementation helps avoid reexamination and iterative redesign after deployment. Whether it's a minor hiccup or a critical flaw, identifying these issues in a smaller implementation will save your organization from the costly and time-consuming process of reevaluating and redesigning once the process is already in place.
8. Continuously improve and monitor the process after deployment
Once fully implemented, measure the new process for efficiency and effectiveness. As market conditions and business operations change, so do business processes. Therefore, a business process requires continuous evaluation and monitoring to ensure it's delivering more value compared to the old process. Gather feedback from stakeholders and monitor the process for any new pain points that need to be addressed.
Mastering process improvement and optimization
Improving and optimizing business processes may seem like a daunting task, but it doesn't have to be. By starting with optimizing single processes, involving stakeholders, and setting realistic and achievable goals your likelihood of success will be high. For those organizations willing to embrace the change and continue to evolve their processes as the business grows and evolves, the rewards are profound: more streamlined workflows, higher cost savings, more operational efficiency, and enhanced customer and employee satisfaction.